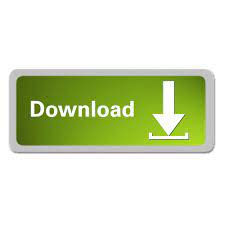
Therefore, ultrasonic dispersers are the most common equipment to produce nano-reinforced composites. Ultrasonication is proven to be highly effective on dispersing nano particles uniformly into slurries. When the ultrasonic filtration process is combined with the addition of inoculants, a simultaneous grain refinement is achieved. (2014: 120ff.) has shown that ultrasonic filtration makes it possible to purify the aluminium alloys AA2024, AA7055, and AA7075 using multi-layered glass fibre filters (with up to 9 layers) with 0.6×0.6mm mesh pores. Due to the enhanced purity of the alloy, the formation of hydrogen pores at the oxides is avoided, so that the fatigue strength of the alloy is increased.Įskin et al. In this case, the filter capillaries retain even nonmetallic impurities of 1–10μm. However, under ultrasonically-assisted filtration the melt is enabled to pass the mesh pores due to the sonocapillary effect. Under common conditions, the melt cannot pass a two-layered filter with a very narrow pore size of 0,4-0,4mm. The smaller the mesh size, the better is the filtration result. glass fibre) to separate unwanted inclusions. During filtration, the melt passes various meshes (e.g. 2014: 120ff.)įiltration is used to remove non-metallic impurities from the melt. The ultrasonic capillary effect (UCE) in liquid metals is the driving effect to remove oxide inclusions during the ultrasonically-assisted filtration of melts. Moreover, the process of mold filling is improved due to lower viscosity of the melt. Industrial power ultrasound systems count as the best amongst other commercial degassing methods regarding effectiveness and processing time. Ultrasonic degasification of aluminum alloys raise the ultimate tensile strength and ductility of the material. Ultrasonic degassing reduces the porosity of the metal achieving thereby a higher material density in the final metal / alloy product. Acoustic flow and streaming assist the floating of these bubbles to the surface and out of the melt, so that the gas can be removed and the gas concentration in the melt is reduced. Due to the formation of larger hydrogen bubbles, the gas bubbles rise. These vacuum bubbles act as nuclei for the formation of hydrogen and vapor bubbles. During the low pressure cycles, tiny vacuum bubbles occur in the liquid or slurry. The acoustic cavitation creates alternating low pressure / high pressure cycles. Ultrasonic Degassing of Metallic Alloysĭegassing is another important effect of power ultrasonics on liquid and semi-solid metals and alloys. The cavitation shock waves assist the breakage of those melting roots. Convection can promote dendrite fragmentation due to extreme local temperatures as well as composition variations and promotes diffusion of solute. UST generates strong convection (heat transfer by mass motion of a fluid) and shock waves in the melt, so that the dendrites are fragmented. 2017)ĭendrite fragmentation: The melting of dendrites usually begins at the root due to local temperature rise and segregation. Macrostructure of Ti alloy after ultrasonic treatment (Ruirun et al. Because those nucleation points are ahead of the solidification front, the growth of dendritic structures does not occur. Those impurities turn into nucleation sites, which are the starting points of solidification. Ultrasonic cavitation causes the even wetting of non-metallic impurities in the melt. Ultrasonic treatment (UST) of melts result in a heterogeneous nucleation and the fragmentation of dendrites, so that the final product shows a significantly higher grain refinement. Ultrasonically altered grain nucleation: Acoustic cavitation and its intense shear forces increase the nucleation sites and number of nuclei in the melt. The formation of non-dendritic structures during solidification of metal melts influences the material properties such as strength, ductility, toughness, and/or hardness. Last but not least, power ultrasound improves the quality of castings.Furthermore, power ultrasound can be used purposefully to reduce the metal porosity or to produce meso-porous structures.Sonication has significant benefits on the microstructural refinement of dendritic grains and primary intermetallic particles.Ultrasonic promotes the non-dendritic solidification in liquid and semi-solid metals.Power ultrasound in molten metals and alloys shows various beneficial effects such as structuring, degassing, and improved filtration.
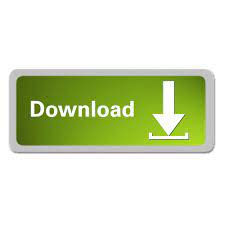